Electromagnetic Slag Detection Machine
Detection of slag in the casting pot and preventing slag from entering the casting operation
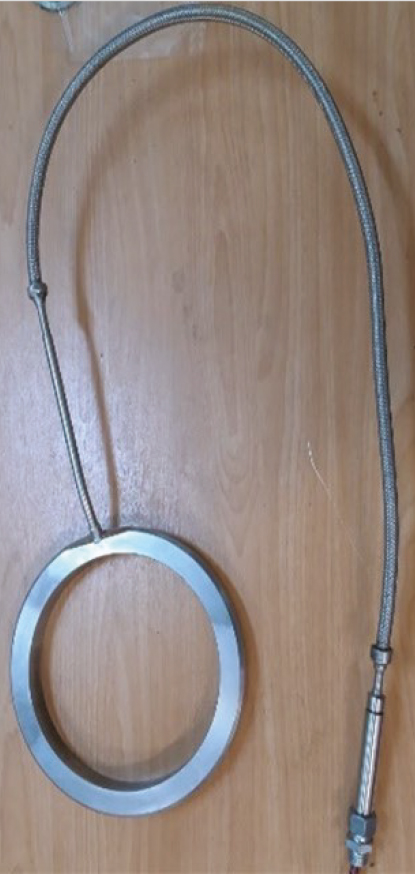
Slag-free transfer of molten steel is critical for prime or scrap and for profit or loss in producing high-quality steels. Regardless of whether it is for furnaces, ladles, or distributors: Large quantities of slag must never be transferred to the next vessel. The ESD Electromagnetic Slag Detection, positioned at the ladle bottom, sounds an alarm when slag flows through and automatically sends a signal to close the slide gate.
The sensor is installed in the outlet opening of the pot and through a transmitter installed in the field, it sends the characteristics of the melt passing through the passage of the pot to the terminal board and the slag detection system in the control room. This sensor works based on magnetic field and voltage induction from primary to secondary. The primary coil is excited by an AC electric current, generated by the slag detection system. The voltage of the secondary winding depends on the type of material passing through the bottle outlet. Therefore, the molten steel creates a different voltage compared to the induced voltage during the passage of slag, and the slag detection system reveals this difference.
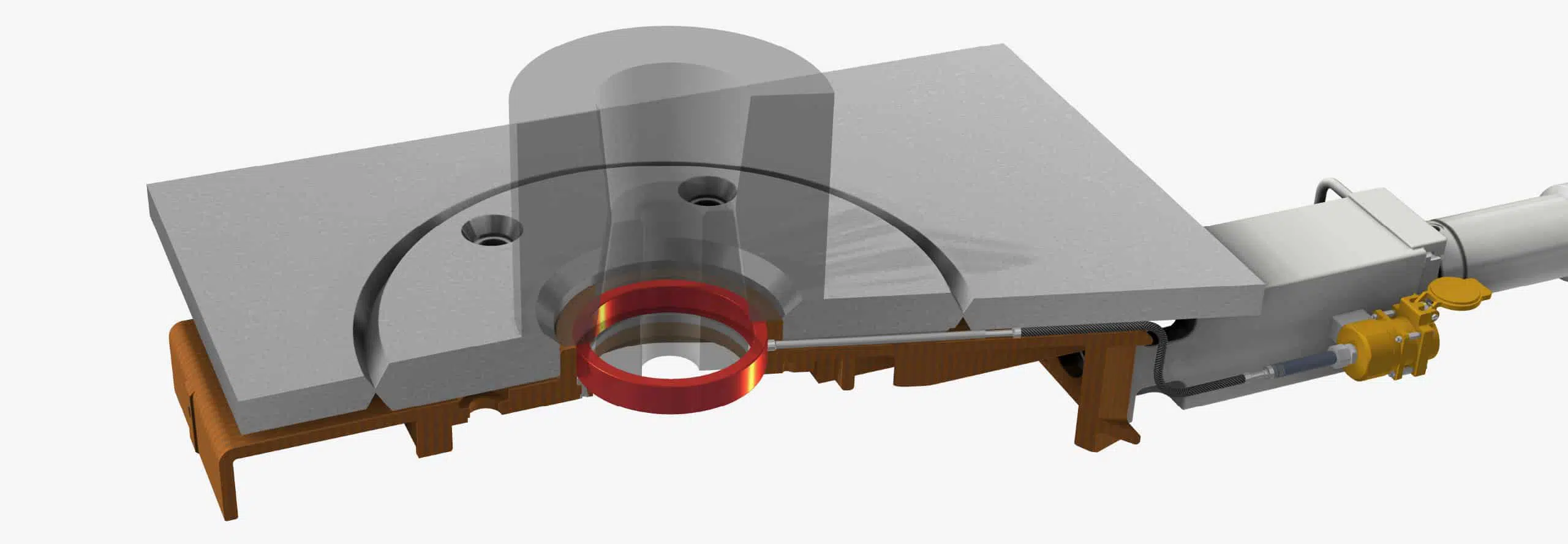
Slag Detection System
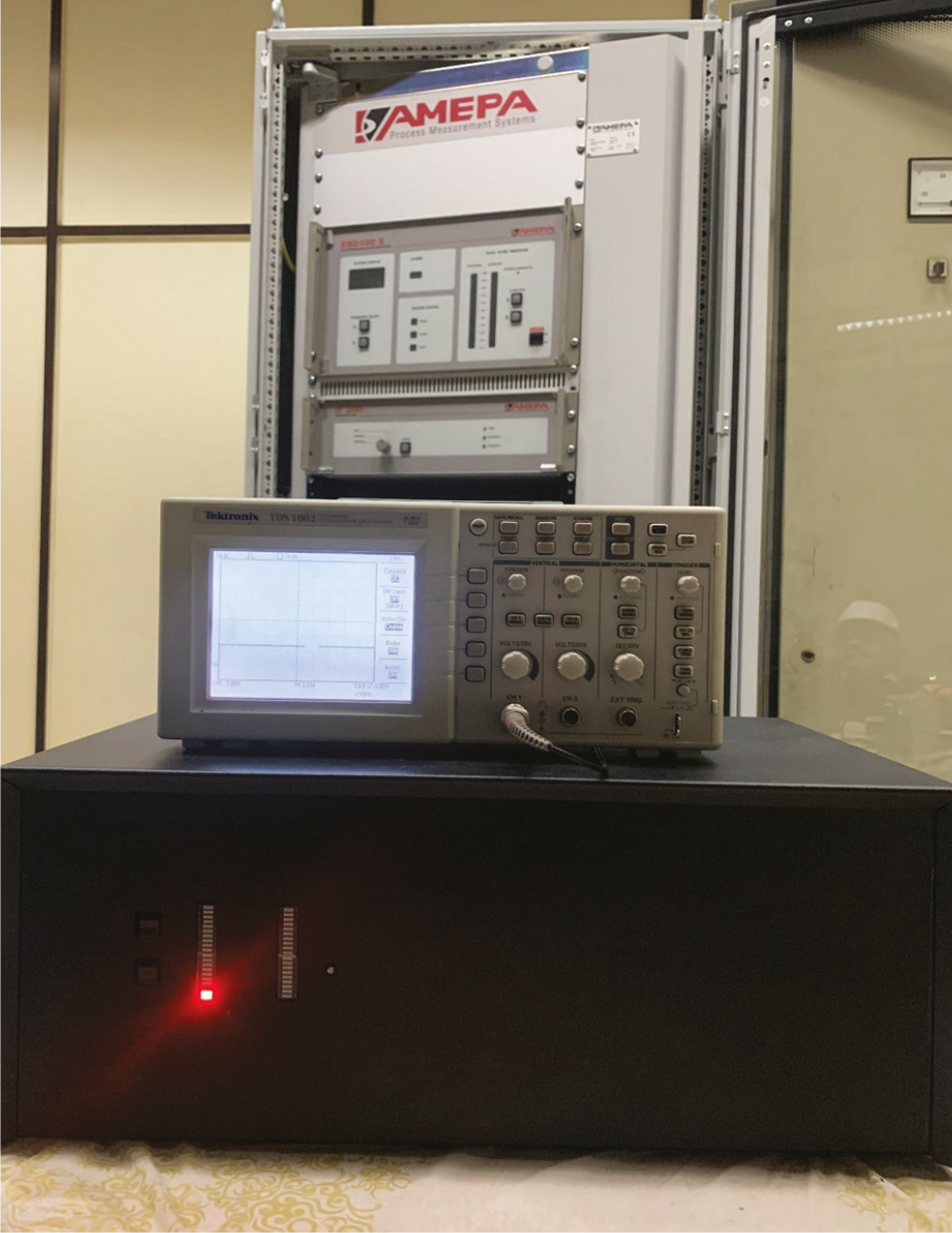
The slag detection system compares the signal received from the secondary sensor with the primary excitation signal and displays the slag percentage in terms of the standard current of 20-4mA in its output. There is also an LED string installed in front of the device that shows the percentage of slag at any moment.
Also, the Slag Set-Point reference value is set with two keys on the front of the device, and the reference value is displayed on the left LED string.
As soon as the amount of slag at the bottle outlet reaches the Slag Set-Point percentage, a Normally Open relay contact is activated and closed. This contact is sent both to the foundry control system, to the command to close the melt exit slide gate, and to the local panel and siren in the foundry operator's pulpit. This contact can be connected to a PLC system or any desired system.
The standard current output of 4-20mA, which shows the percentage of slag as a continuous value, is active during the whole process of emptying the bottle, which displays the percentage of slag and sends it to the control system and PLC. The analog output channel of the slag detection system can be connected to any standard analog input channel.
Performance Test
At different stages of designing and manufacturing the machine and its sub-sections, tests were carried out in the casting unit of Esfahan's Mobarakeh Steel Company. After completing the construction steps and making the final settings, in March 2023, the final functional test in this unit was successfully performed on casting machine No. 3.
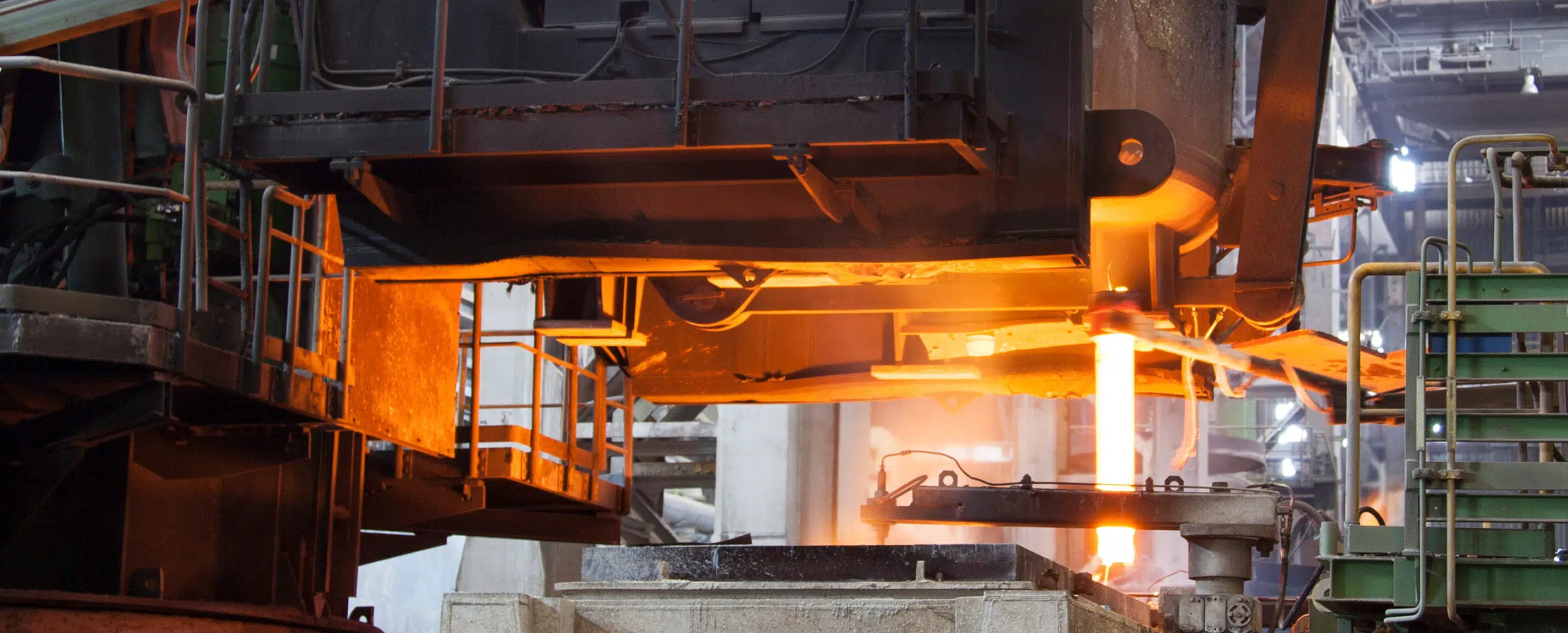
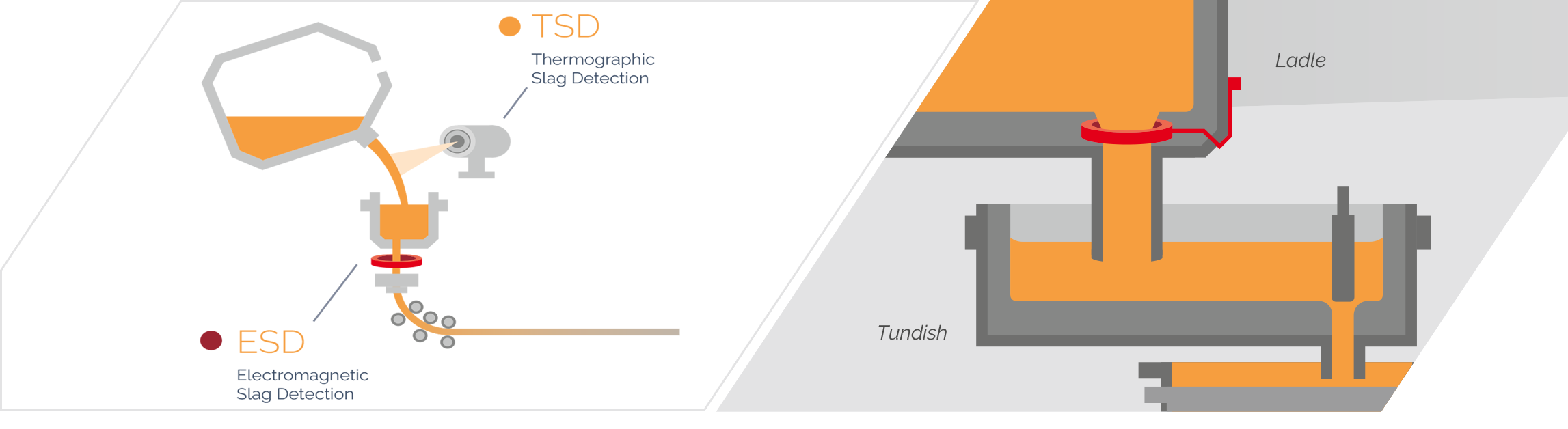
Structure and Main Components of System
Advantages
- Product quality increases due to the automatic prevention of slag entering the production products in the casting line
- Increasing productivity and reducing the production cost due to clogging of shroud's path and cleaning tundish from slag
- Eliminate human error (which is unavoidable in a manual system)
- Slag detection device with high accuracy and sensitivity, similar to AMEPA type ESD100 device
- Electromagnetic detection method
- Changeable detection sensitivity with different grades
- The device is compatible with magnetic sensors
- The slag detection system detects correct operation and faults.
- The slag detection system includes the main standing panel (with cooling system), amplifier, and operator panel.
- The system is protected against strong noises on site (due to EAF furnaces).
- The operator panel provides the same displays and commands as the AMEPA operator panel.
- The user software of the device is highly reliable and can network and connect to a laptop.
- All system faults are coded and displayed on the monitor installed on the main board.
- The main panel of the slag detection system has the following sub-systems and parts:
- Main control and processing section (similar to MCU100)
- Power supplies, hardware intermediates similar to IF200
- Displays and digital recorder
- Interface card with HMI and operator panel
- Signaling terminals
- Power terminals
- Communication intermediary with sensor amplifier (similar to PA100)
- Sensor excitation drive cards
- Input and output cards to connect to the PLC in the automation system
- Safety and protection subsystems and ESD
- Diagnostics and alarms subsystem
- Analog Output
- 4-20 mA
- Reduction of the quantity of slag
- up to 90%
- Increasing the yield
- ~1%
- Less clogging of the SEN
- Up to 60%
Brochure
2.17MB
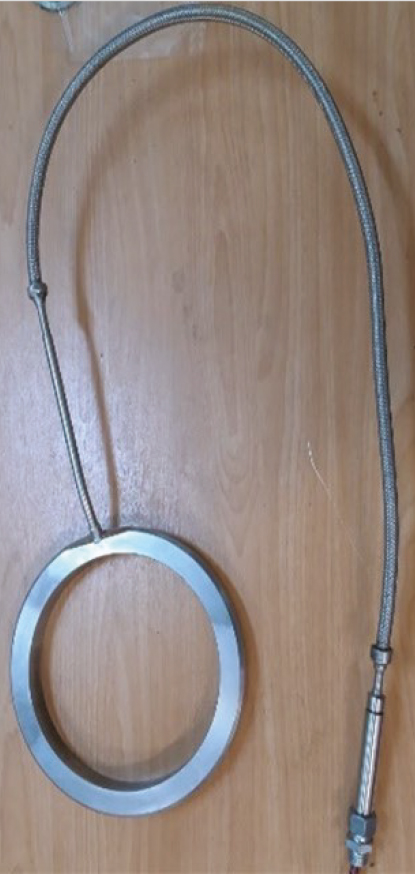
Slag-free transfer of molten steel is critical for prime or scrap and for profit or loss in producing high-quality steels. Regardless of whether it is for furnaces, ladles, or distributors: Large quantities of slag must never be transferred to the next vessel. The ESD Electromagnetic Slag Detection, positioned at the ladle bottom, sounds an alarm when slag flows through and automatically sends a signal to close the slide gate.
The sensor is installed in the outlet opening of the pot and through a transmitter installed in the field, it sends the characteristics of the melt passing through the passage of the pot to the terminal board and the slag detection system in the control room. This sensor works based on magnetic field and voltage induction from primary to secondary. The primary coil is excited by an AC electric current, generated by the slag detection system. The voltage of the secondary winding depends on the type of material passing through the bottle outlet. Therefore, the molten steel creates a different voltage compared to the induced voltage during the passage of slag, and the slag detection system reveals this difference.
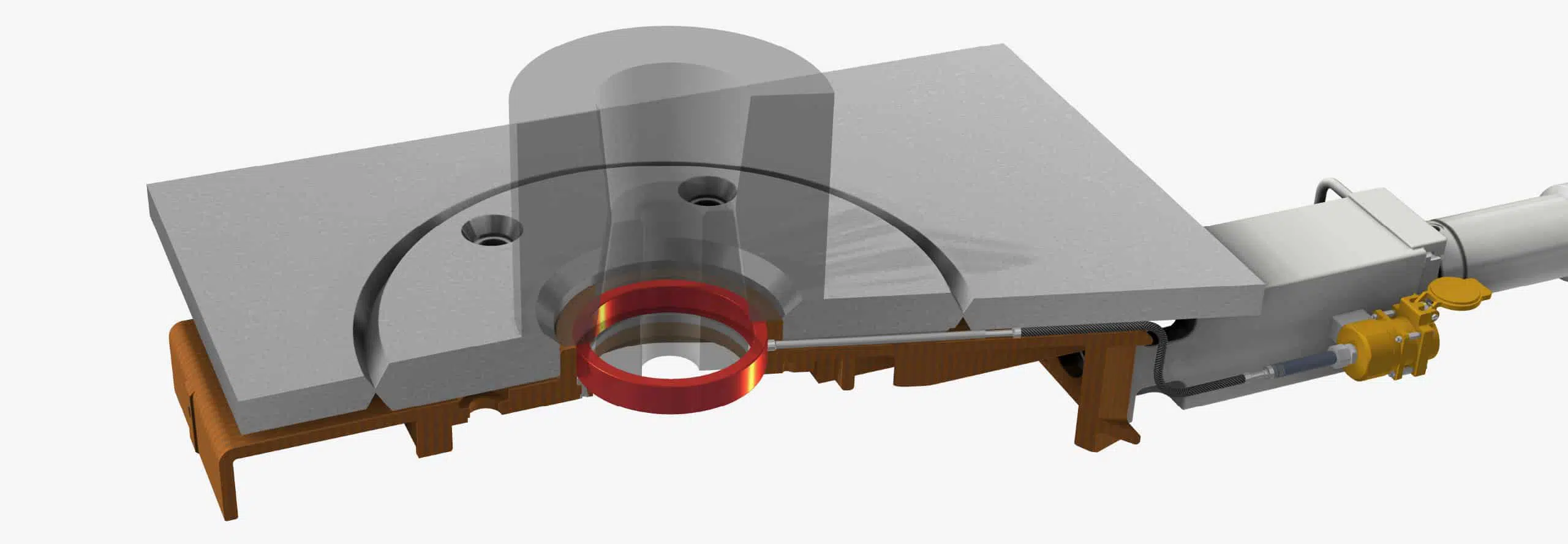
Slag Detection System
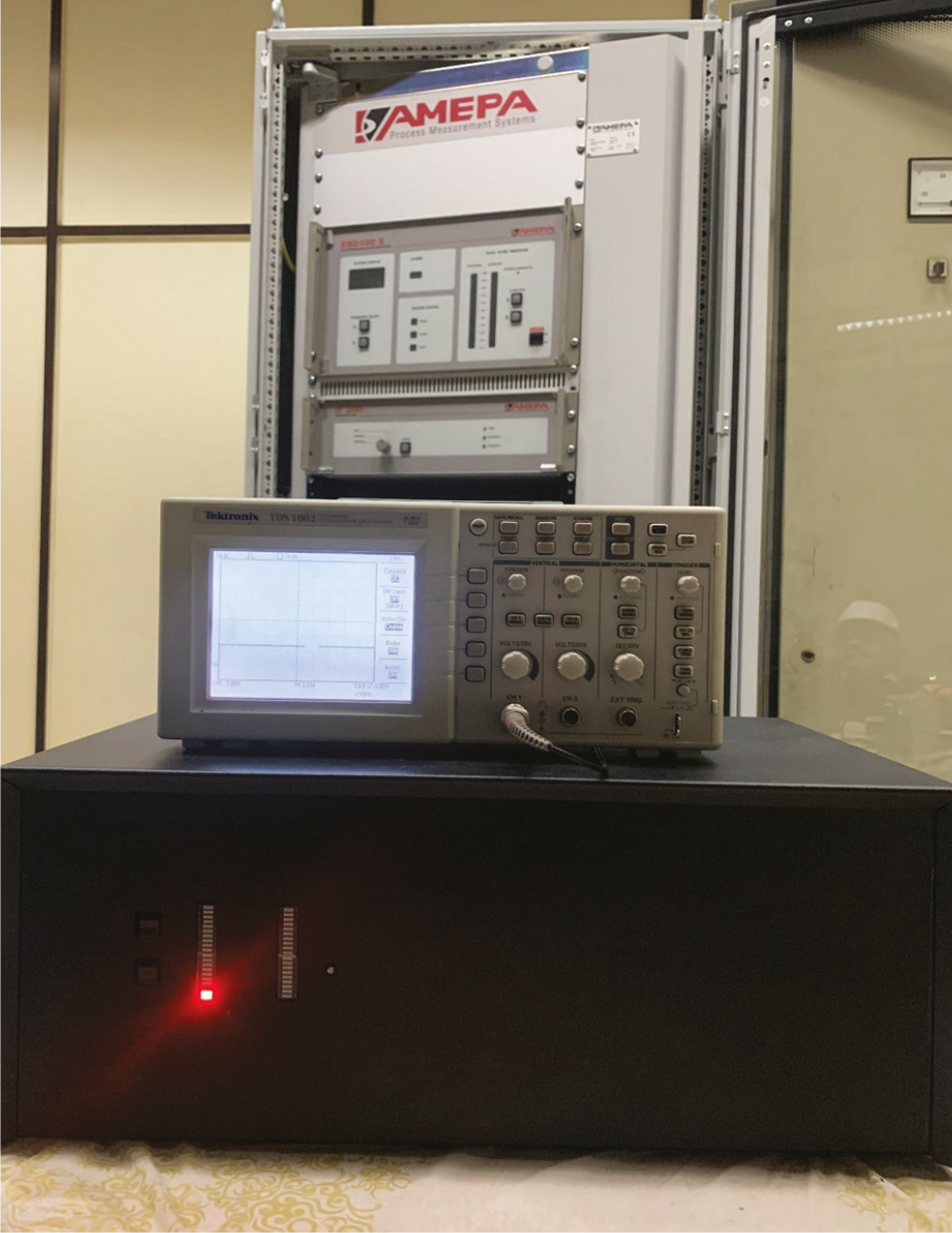
The slag detection system compares the signal received from the secondary sensor with the primary excitation signal and displays the slag percentage in terms of the standard current of 20-4mA in its output. There is also an LED string installed in front of the device that shows the percentage of slag at any moment.
Also, the Slag Set-Point reference value is set with two keys on the front of the device, and the reference value is displayed on the left LED string.
As soon as the amount of slag at the bottle outlet reaches the Slag Set-Point percentage, a Normally Open relay contact is activated and closed. This contact is sent both to the foundry control system, to the command to close the melt exit slide gate, and to the local panel and siren in the foundry operator's pulpit. This contact can be connected to a PLC system or any desired system.
The standard current output of 4-20mA, which shows the percentage of slag as a continuous value, is active during the whole process of emptying the bottle, which displays the percentage of slag and sends it to the control system and PLC. The analog output channel of the slag detection system can be connected to any standard analog input channel.
Performance Test
At different stages of designing and manufacturing the machine and its sub-sections, tests were carried out in the casting unit of Esfahan's Mobarakeh Steel Company. After completing the construction steps and making the final settings, in March 2023, the final functional test in this unit was successfully performed on casting machine No. 3.
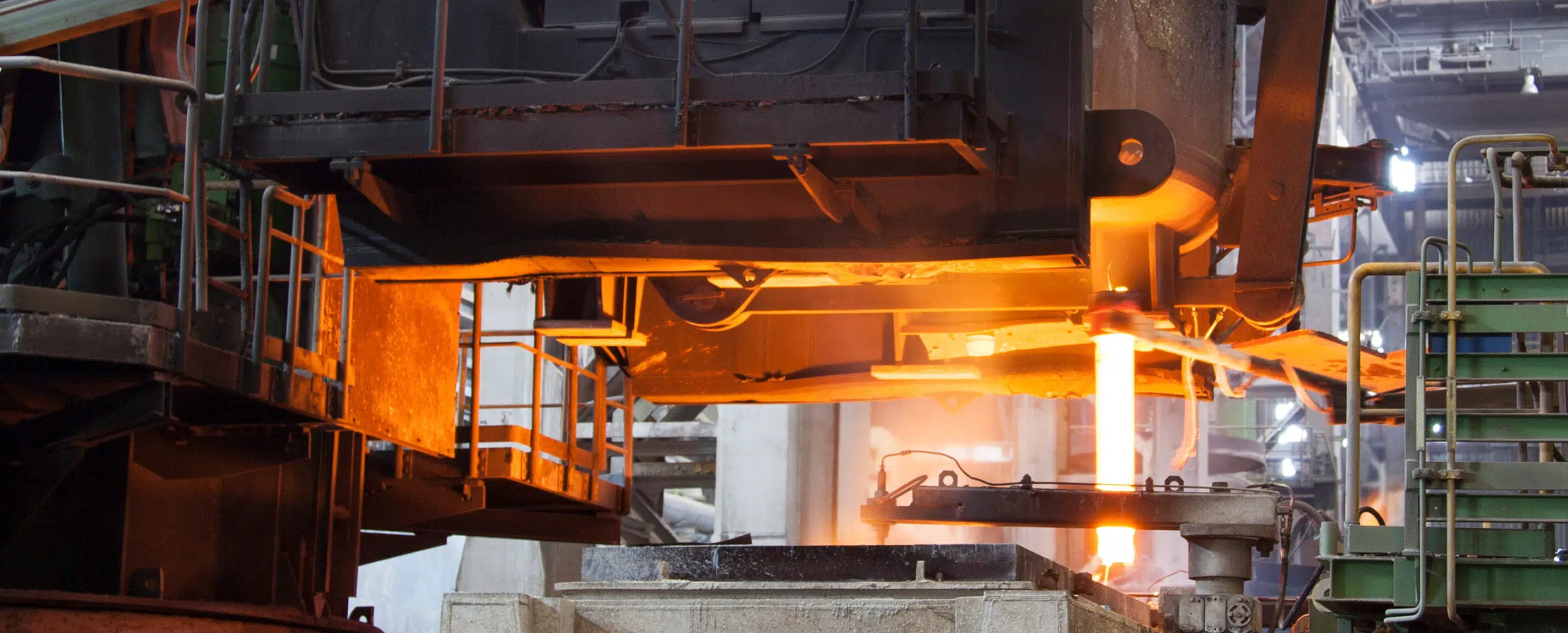
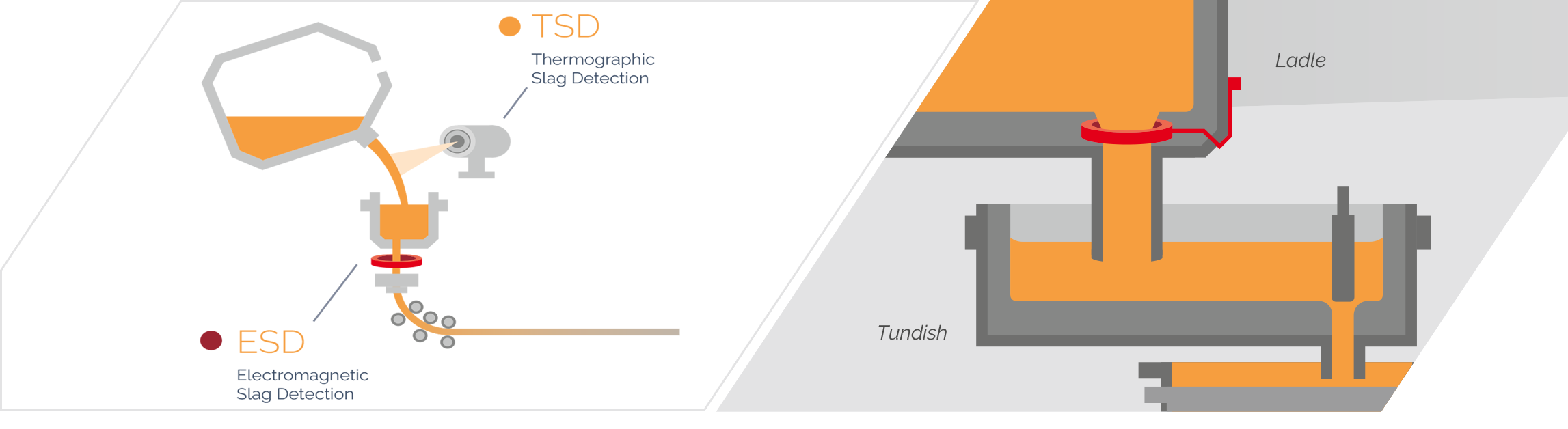
Structure and Main Components of System
Advantages
- Product quality increases due to the automatic prevention of slag entering the production products in the casting line
- Increasing productivity and reducing the production cost due to clogging of shroud's path and cleaning tundish from slag
- Eliminate human error (which is unavoidable in a manual system)
- Slag detection device with high accuracy and sensitivity, similar to AMEPA type ESD100 device
- Electromagnetic detection method
- Changeable detection sensitivity with different grades
- The device is compatible with magnetic sensors
- The slag detection system detects correct operation and faults.
- The slag detection system includes the main standing panel (with cooling system), amplifier, and operator panel.
- The system is protected against strong noises on site (due to EAF furnaces).
- The operator panel provides the same displays and commands as the AMEPA operator panel.
- The user software of the device is highly reliable and can network and connect to a laptop.
- All system faults are coded and displayed on the monitor installed on the main board.
- The main panel of the slag detection system has the following sub-systems and parts:
- Main control and processing section (similar to MCU100)
- Power supplies, hardware intermediates similar to IF200
- Displays and digital recorder
- Interface card with HMI and operator panel
- Signaling terminals
- Power terminals
- Communication intermediary with sensor amplifier (similar to PA100)
- Sensor excitation drive cards
- Input and output cards to connect to the PLC in the automation system
- Safety and protection subsystems and ESD
- Diagnostics and alarms subsystem
- Analog Output
- 4-20 mA
- Reduction of the quantity of slag
- up to 90%
- Increasing the yield
- ~1%
- Less clogging of the SEN
- Up to 60%
Brochure
2.17MB